Wesley A. Tayon, PhD
- wtayon@technoirva.com
- Jan 4, 2024
- 4 min read
Updated: 17 hours ago
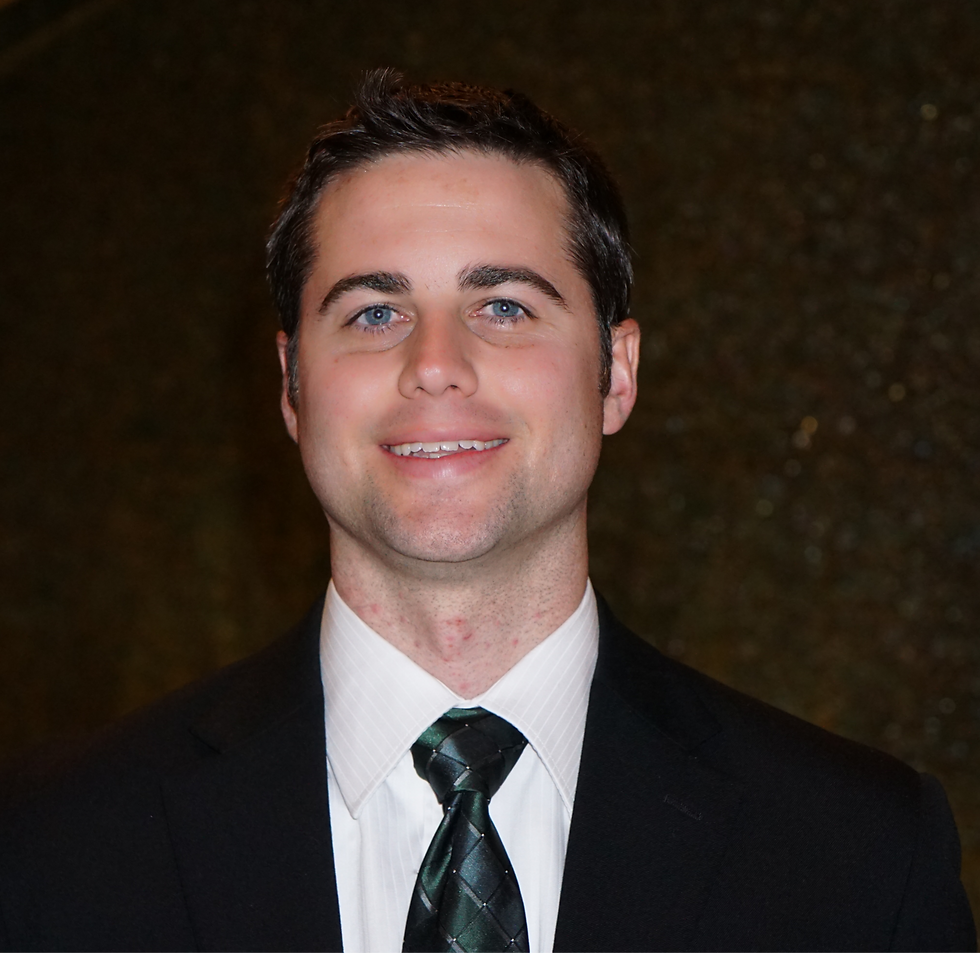
SUBJECT MATTER EXPERTISE
Metallic Materials
Microscopy
Failure Analysis
Microstructural Characterization
Texture Analysis
Mechanical Behavior of Materials
Advanced Manufacturing
Physical Metallurgy
Crystal Plasticity
LANGUAGE FLUENCY
English
PROFESSIONAL MEMBERSHIPS, LICENSES, AND SKILLS:
ASM International - The American Society for Metals
CURRICULUM VITAE
Wesley Tayon is a Materials Research Engineer in the Advanced Materials and Processing Branch at NASA Langley Research Center. Dr. Tayon holds B.S., M.S. and Ph.D. degrees in Mechanical Engineering from Old Dominion University, the University of Illinois at Urbana-Champaign, and the University of Utah, respectively. His work at NASA Langley involves developing and evaluating advanced structural materials and processing methods for aircraft and spacecraft structures. He serves on the NASA NESC Materials Technical Discipline Team—a group of approx. 70 recognized materials engineering experts from across the country.
Over his 15+ year career at NASA, he has provided innovative solutions to complex aerospace materials issues in the areas of advanced manufacturing, materials processing, characterization, mechanical property evaluation, and failure analysis to support advanced aerospace materials and structures development. He has experience in advanced materials characterization techniques, such as electron microscopy, X-ray diffraction, elemental analysis, and microstructure characterization using electron backscattered diffraction (EBSD).
Dr. Tayon has authored or co-authored over 14 journal articles, 12 NASA technical reports, 11 conference papers and 44 conference presentations. His publications have received approximately 600 citations to date. A recent co-authored paper was awarded the 2024 Top Cited Paper Award in North America within the Materials category from IOP Publishing. He also was recently awarded the NASA Exceptional Technology Achievement Medal in 2024, along with several NASA Group Achievement Awards over his career.
EDUCATION
Old Dominion University, B.S. in Mechanical Engineering – 2009
University of Illinois at Urbana-Champaign, M.S. in Mechanical Engineering – 2012
University of Utah, Ph.D. in Mechanical Engineering – 2023
COMPUTER LANGUAGE & PROGRAMS
Python
MATLAB
C++
MS Office
MTEX
OIM (EBSD Analysis Software)
APEX (EDS Analysis Software)
AWARDS
NASA Exceptional Technology Achievement Medal, 2024
Top Cited Paper Award, IOP Publishing North America, Materials, 2024
NASA Group Achievement Award, 2024 – AATT Lightweight Metallic Fuselage Team
Superior Accomplishment Award, 2023 – Outstanding Technical Support and Commitment to the Capacitor Microstructure Analysis/Tools Development Assessment for the NESC
NASA Group Achievement Award, 2023 – Light Alloy Lab (LAL) Return to Work Team
1st Place Team for Microstructure Prediction, 2022 NIST-sponsored AM-Bench Challenge
NASA Group Achievement Award, 2020 – NESC Propellant Tank Safe Life Assessment
NASA Group Achievement Award, 2017 – Integrally Stiffened Cylinder Sounding Rocket Flight
BIOGRAPHY
Dr. Tayon's early research focused on advanced characterization of aluminum-lithium alloys. During his M.S. research, he applied electron backscattered diffraction; in-situ 3D, high-energy, synchrotron X-ray diffraction microscopy; and crystal plasticity finite element modeling to assess the role of texture on the intergranular failure mode known as delamination. His research determined that stress-state, texture, and grain boundary precipitates strongly influenced the location of cracking within the microstructure. His research offers the potential to modify processing of these alloys to reduce this behavior.
Beginning in 2014, Dr. Tayon worked with NASA and industry colleagues to mature a new manufacturing approach for cryogenic fuel tank and aluminum fuselage production known as the Integrally Stiffened Cylinder (ISC) Process. The process utilizes flow forming and a tailored mandrel to manufacture near net-shape, single-piece barrels with internal stiffeners, reducing manufacturing cost and increasing manufacturing rate and structural performance. Dr. Tayon led characterization and testing efforts to help guide process development and heat treatment. In 2015, Dr. Tayon participated in ground testing and sounding rocket flight demonstration of the ISC technology at NASA Wallops Flight Facility. Later, the team led the first commercial scale manufacturing demonstration, producing a 10-ft. diameter ISC in 2019, and subsequent fuselage demonstration article in 2021. Dr. Tayon's research helped motivate NASA Langley to purchase an R&D spin/flow forming machine in 2021, where he is actively working to improve the spin/flow forming process today in collaboration with US industry partners.
In 2022, Dr. Tayon joined the NASA Engineering and Safety Center (NESC) Materials Technical Discipline Team (TDT). The Materials TDT is comprised of ~70 recognized experts from NASA, other government agencies, industry, and academia to support NASA missions when additional expertise is needed to ensure safety or solve complex problems.
In 2023, Dr. Tayon completed his Ph.D. from the University of Utah. His research focused on in-situ characterization, testing, and modeling techniques for advanced manufacturing challenges at NASA. Topics included assessment of the role of texture on slip systems softening due to planar slip in aluminum-lithium alloys using in-situ, high-energy X-ray diffraction microscopy; application of in-situ digital image correlation to correlate material performance with flow formability in aerospace aluminum alloys; and computational simulation of the effect of residual stresses on fatigue performance of additively manufactured Inconel alloy 625 using in-situ, high-energy X-ray diffraction microscopy and crystal plasticity finite element modeling.
In 2024, Dr. Tayon was awarded the NASA Exceptional Technology Achievement Medal for his contributions in advanced aerospace metallurgical processes and characterization.